The Complete Guide to Rotating Hydraulic Couplings
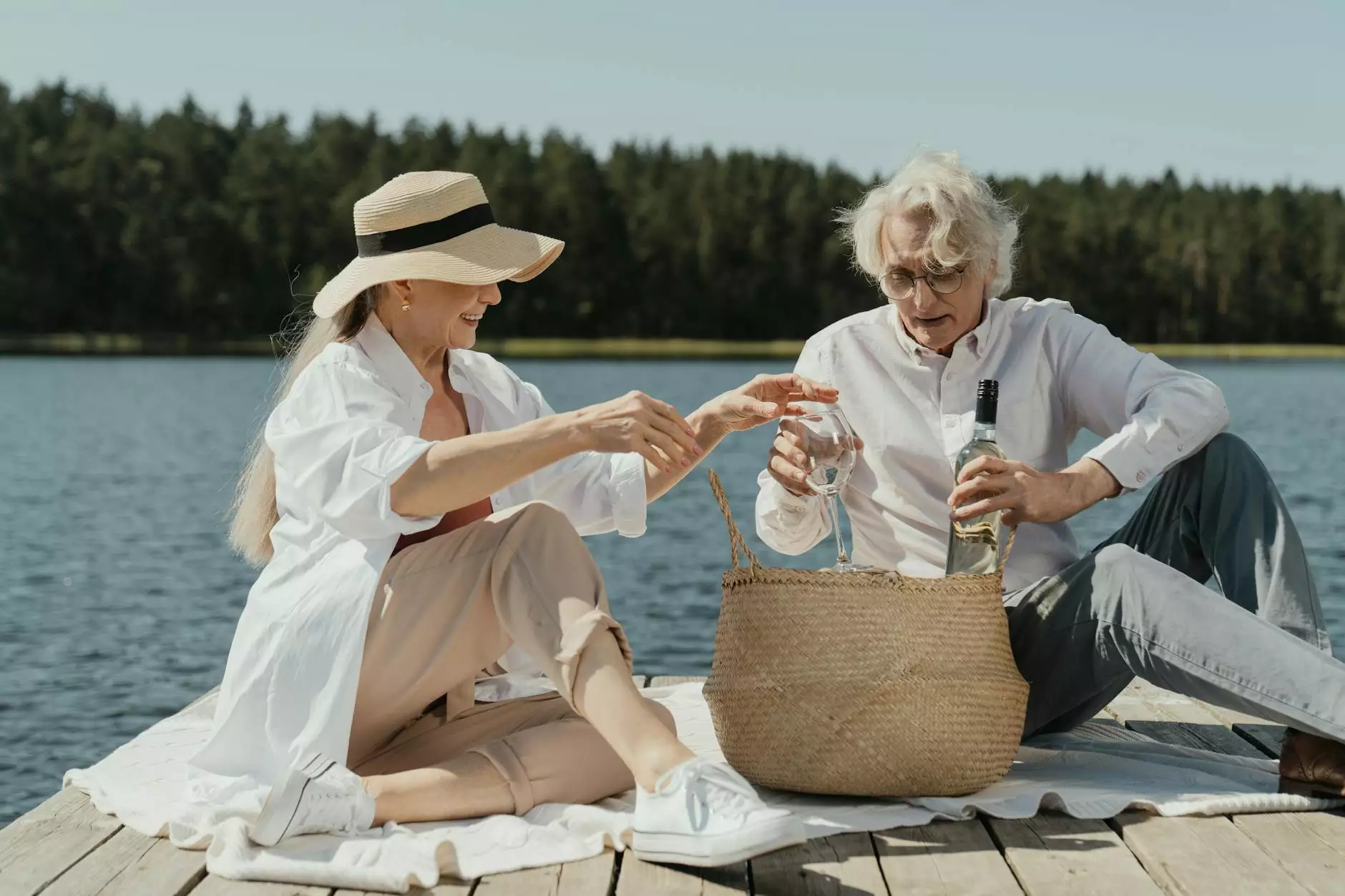
In the evolving landscape of industrial machinery, the role of components such as rotating hydraulic couplings cannot be overstated. These innovative devices have transformed numerous industries by enabling efficient power transmission, fluid control, and operational flexibility. In this comprehensive guide, we will explore the significance, applications, and technical specifications of rotating hydraulic couplings, aimed particularly at business professionals and engineers.
What is a Rotating Hydraulic Coupling?
A rotating hydraulic coupling serves as a connector between two hydraulic circuits, allowing fluid to flow while preventing the transfer of torque between the components. The design permits rotary motion to occur while maintaining a seal that protects the system from leakage. This feature is crucial in applications where rotational motion is necessary, such as in drive shafts and rotary drum machinery.
Key Advantages of Rotating Hydraulic Couplings
Using rotating hydraulic couplings presents several benefits from an operational and efficiency perspective:
- Enhanced Flexibility: They allow for a degree of movement in machinery, accommodating misalignments and vibrations.
- Reduced Wear and Tear: By minimizing friction and mechanical stress, they contribute to longer equipment life.
- Improved Safety: These couplings can maintain proper fluid levels and prevent leaks, enhancing operational safety.
- Higher Efficiency: With reduced energy losses, they optimize fluid power systems leading to reduced operational costs.
Applications of Rotating Hydraulic Couplings
The versatility of rotating hydraulic couplings enables their application across diverse sectors. Here are some notable industries where these couplings prove indispensable:
- Construction: Used in excavators, cranes, and concrete mixers, these couplings facilitate the complex fluid dynamics required for heavy machinery.
- Marine: In vessels, they play a crucial role in propulsion systems, enabling the transfer of power while maintaining fluid integrity.
- Aerospace: Rotating hydraulic couplings are vital in aircraft systems where reliable fluid transfer is necessary for hydraulic controls.
- Manufacturing: They are employed in automation and robotic systems, providing efficient torque transmission while maintaining flexibility.
Technical Specifications of Rotating Hydraulic Couplings
Understanding the technical specifications of rotating hydraulic couplings is essential for making informed purchasing decisions. Here are some critical parameters to consider:
1. Pressure Ratings
Couplings are designed to operate under various pressure levels. It's crucial to match the coupling with the operational pressure of your hydraulic system to prevent failures.
2. Temperature Range
The operating temperature can significantly influence the coupling's performance. Ensure the coupling can withstand the specific temperatures involved in your application.
3. Material Composition
Typically constructed from high-grade materials such as steel, stainless steel, or specialized alloys, the choice of material affects durability and performance.
4. Size and Dimensions
The physical dimensions of the coupling need to fit the existing machinery without requiring extensive modifications.
How to Choose the Right Rotating Hydraulic Coupling
Selecting the appropriate rotating hydraulic coupling can significantly impact the performance of your hydraulic systems. Here are several guiding factors:
- Assess Your Application: Understand the specific needs of your machinery, including pressure, temperature, and space constraints.
- Consult the Experts: Engage with manufacturers or suppliers, such as fitsch.cn, to gain insights on the best options for your operational needs.
- Evaluate Performance Data: Look for performance ratings and durability assessments to ensure long-term reliability.
- Review Warranty and Support: A comprehensive warranty and robust customer support can be indicative of product quality.
Maintaining Rotating Hydraulic Couplings
To ensure optimal functionality and longevity of rotating hydraulic couplings, regular maintenance is essential:
- Regular Inspections: Frequent checks for signs of wear, leaks, or corrosion can prevent larger issues.
- Fluid Quality: Ensure that the hydraulic fluid is clean and suitable for the operating conditions.
- Proper Lubrication: Adequate lubrication can enhance performance and reduce the risk of friction-related failures.
- Components Replacement: Keep a schedule for replacing couplings based on the manufacturer's recommendations and operational history.
The Future of Rotating Hydraulic Couplings
As technology progresses, we can expect advancements in rotating hydraulic couplings. Innovations will likely include:
- Smart Technology: Integration with sensors for real-time monitoring of pressure, temperature, and performance.
- Enhanced Materials: Development of lighter and more durable materials designed to withstand extreme conditions.
- Automation: Utilizing automation for easier coupling connection and disconnection in complex machinery.
Conclusion
In conclusion, rotating hydraulic couplings are essential components that contribute significantly to operational efficiency across various industries. Their ability to provide flexibility, enhance safety, and reduce wear makes them a valuable asset in any hydraulic system. As we look to the future, advancements in technology and materials will continue to reshape how these couplings are designed and implemented, leading to even greater efficiencies in fluid power systems.
For businesses seeking reliable hydraulic solutions, consider exploring the product offerings at fitsch.cn. With a commitment to quality and innovation, fitsch.cn is dedicated to providing the best fittings for sale, keeping your operations running smoothly and efficiently.