Leveraging Prototype Moulds in Metal Fabrication
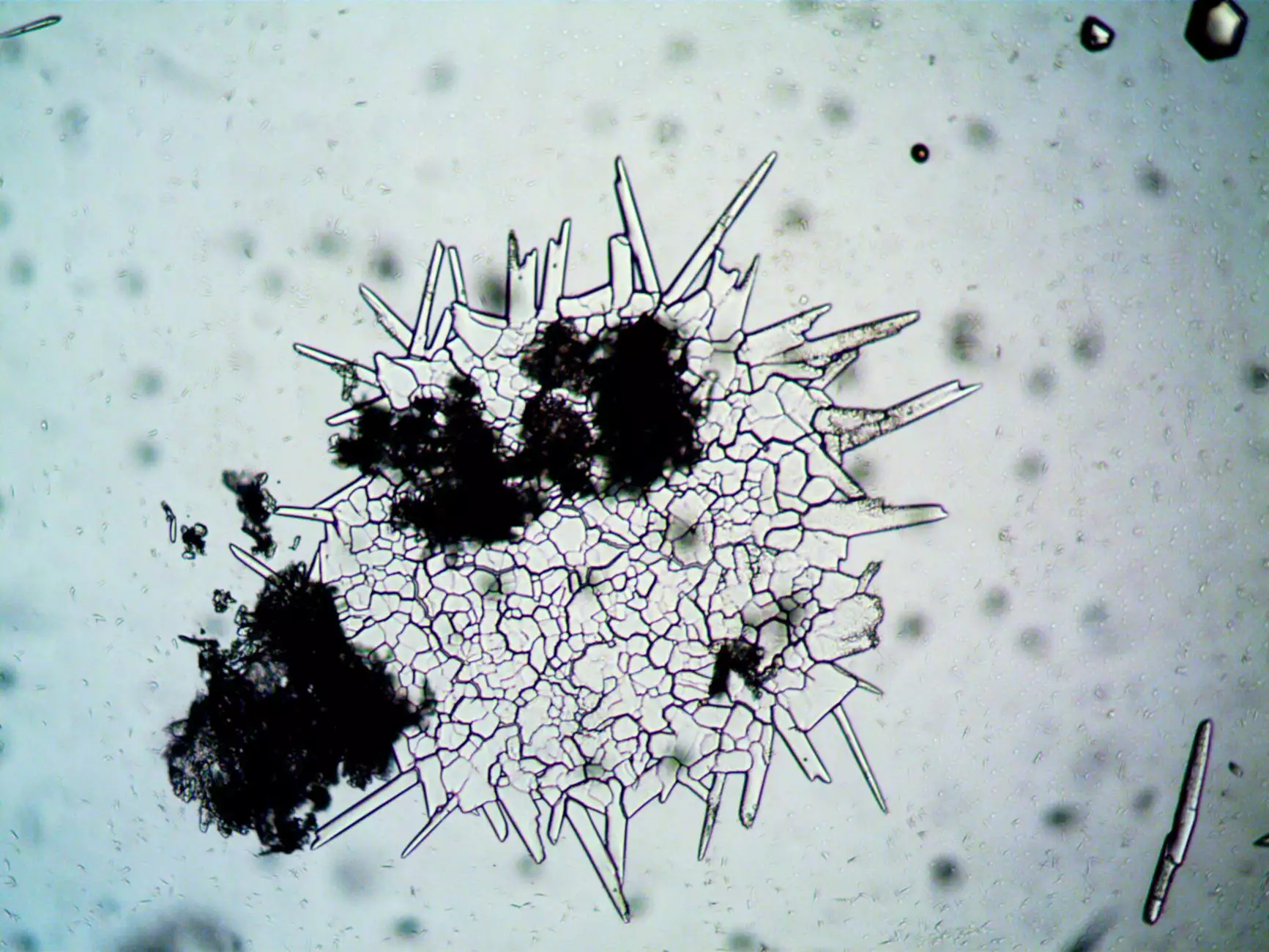
The demand for precision and efficiency in manufacturing has never been higher. Businesses are constantly searching for innovative methods to enhance productivity and reduce costs. Prototype moulds have emerged as a game-changer in the field of metal fabrication, providing unparalleled advantages. In this article, we will explore what prototype moulds are, their benefits, applications in various industries, and how they are transforming the manufacturing landscape.
What is a Prototype Mould?
A prototype mould is a specialized form of tooling used in the manufacturing process designed to create multiple identical parts from a chosen material, typically metal or plastic. These moulds serve as templates for producing parts in bulk with high precision. The primary objective of employing prototype moulds is to streamline production while ensuring the quality and consistency of the final products.
Types of Prototype Moulds
There are several types of prototype moulds, each serving different purposes based on the manufacturing requirements:
- Injection Moulds: These are widely used in plastic manufacturing, but specialized versions can also be used in metal applications.
- Compression Moulds: Suitable for producing thicker parts and often used in industries needing robust components.
- Blow Moulds: Mainly utilized for products that require hollow designs, such as bottles and containers.
- Die Casting Moulds: Used for low-pressure die casting applications, giving detailed and intricate shapes.
Benefits of Using Prototype Moulds
Utilizing prototype moulds in metal fabrication comes with a myriad of benefits that can significantly influence the overall manufacturing process:
1. Cost Efficiency
Creating parts using prototype moulds can drastically lower production costs. Traditional manufacturing methods may incur high labor and material costs, but with moulds, the process can be automated. Moreover, the ability to produce multiple parts simultaneously reduces the cost per unit.
2. Improved Precision and Quality
One of the standout features of prototype moulds is their precision. The moulds are engineered to ensure that every part produced is identical to the last, maintaining consistency in quality. This is crucial in industries where tolerances are tight, and performance standards must be met, such as aerospace and automotive.
3. Speed of Production
Time is a critical factor in business. Prototype moulds facilitate rapid production cycles, enabling manufacturers to bring products to market quicker. The efficiency gained allows companies to respond rapidly to market demands and customer needs, keeping them ahead of the competition.
4. Flexibility and Adaptability
In today's fast-paced business environment, the ability to adapt is paramount. Prototype moulds can be modified easily to accommodate design changes, providing companies with the flexibility needed to evolve their products without incurring substantial costs.
Applications of Prototype Moulds in Various Industries
Prototype moulds find applications across multiple industries, highlighting their versatility:
1. Automotive Industry
The automotive sector relies heavily on prototype moulds for producing components with precision. Parts like housings, brackets, and gears are manufactured using different moulding techniques to meet stringent safety and performance standards.
2. Aerospace Industry
In the aerospace industry, where weight reduction and strength are of utmost importance, prototype moulds are used to produce lightweight yet strong components. This ensures fuel efficiency and overall performance enhancement of aircraft.
3. Consumer Electronics
The rapid turnover of consumer electronic devices necessitates rapid prototyping and production. Prototype moulds allow manufacturers to create intricate designs while maintaining the integrity and durability of the components.
4. Medical Devices
In the medical field, precision and safety are paramount. Prototype moulds are employed to manufacture surgical instruments and components for medical devices with precision that meets regulatory standards.
Implementing Prototype Moulds in Your Business
To successfully integrate prototype moulds into your business operations, consider the following steps:
1. Assess Your Needs
Before implementing prototype moulds, conduct a thorough assessment of your production processes. Determine the types of parts that require moulding and identify areas where you can benefit from increased efficiency.
2. Choose the Right Moulds
Select the type of mould that best fits your needs. Factors to consider include the material to be used, the complexity of the part design, and the desired rate of production.
3. Partner with a Reputable Manufacturer
Work with a professional mould-making company, such as DeepMould, to ensure you have access to high-quality prototype moulds. Their expertise will help you navigate the technical aspects and optimize your production process.
4. Continually Update and Innovate
Maintain a culture of innovation within your organization. Prototype mould technology is continually evolving; staying updated on the latest advancements can provide you with additional competitive advantages.
Case Studies: Successful Implementations of Prototype Moulds
1. Automotive Manufacturer Success Story
One prominent automotive company implemented prototype moulds in their production line, resulting in a 30% reduction in production time. By investing in advanced moulding technology, they were able to streamline their manufacturing process significantly, which led to cost savings and increased output.
2. Aerospace Innovations
An aerospace parts manufacturer adopted prototype mould technology to produce complex-component geometries that were previously difficult to achieve. This resulted in lighter components that maintained structural integrity, leading to enhanced fuel efficiency in aircraft.
Challenges and Solutions in Prototype Moulding
While the advantages of prototype moulds are clear, there are challenges associated with their use. Here are some common issues and potential solutions:
1. Initial Investment Costs
The initial costs of designing and producing prototype moulds can be significant. However, these costs should be viewed as an investment, given the long-term savings in production costs and increased output. Consider financing options or phased implementations to mitigate upfront expenses.
2. Design Complexity
Designing effective prototype moulds requires expertise. Collaborating with experienced designers and engineers can help overcome this challenge, ensuring that your moulds are not only effective but also efficient in the production process.
The Future of Prototype Moulds in Metal Fabrication
The future of metal fabrication is bright, especially with the continuous advancements in prototype mould technology. We can expect enhanced materials, better design software, and faster production times as technology evolves. Innovations such as 3D printing for mould production and automated moulding processes will further revolutionize the industry.
Conclusion
In summary, prototype moulds are indispensable tools in the world of metal fabrication. Their advantages in cost efficiency, precision, and speed make them ideal for various industries, from automotive to aerospace. By understanding how to implement and leverage these moulds effectively, businesses can position themselves for success in an increasingly competitive market. Embracing this technology not only boosts production capabilities but also fosters innovation and adaptability, essential traits for future growth.
For more insights on how to optimize your manufacturing with prototype moulds, visit DeepMould.