The Impact of Automotive Molds on the Automotive Industry
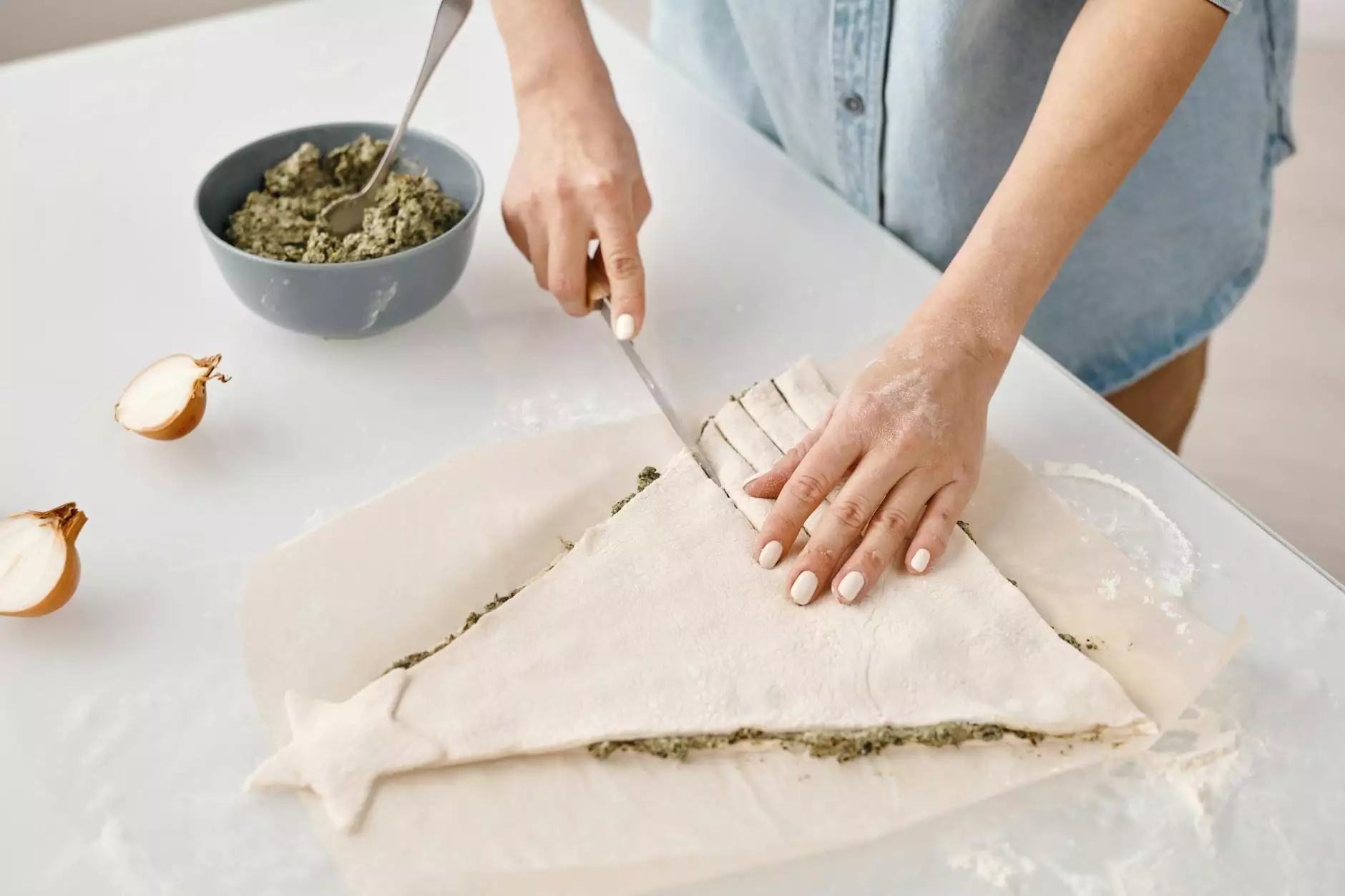
The automotive industry is an ever-evolving landscape, continuously seeking innovation to improve the quality and efficiency of vehicle production. One of the most significant advancements contributing to this evolution is the use of automotive molds. The integration of high-precision molds streamlines manufacturing processes, ensures consistency in production, and enhances the overall quality of finished vehicles. In this article, we will delve into the intricacies of automotive molds, their types, applications, advantages, and their role in shaping the future of automotive manufacturing.
Understanding Automotive Molds
Automotive molds are specialized tools designed to shape materials into specific components used in vehicles. These molds are pivotal in the manufacturing process, as they dictate the final shape, design, and finish of various automotive parts. Using advanced materials and technologies, these molds enable the mass production of complex shapes with high precision—qualities vital for modern automotive design and functionality.
Types of Automotive Molds
There are several types of automotive molds used in the industry today. Each type serves a specific purpose and is tailored to meet the requirements of various automotive components:
- Injection Molds: Most commonly used for creating plastic components, injection molds allow molten plastic to be injected into a mold cavity where it cools and solidifies into the desired shape. This method is ideal for producing large quantities of small to moderately complex parts.
- Blow Molds: Used primarily for producing hollow plastic parts such as fuel tanks and containers, blow molds allow air to be blown into a preformed tube of plastic, expanding it to fit the inner contours of the mold.
- Compression Molds: This method involves placing a preheated material into a heated mold cavity where it is compressed to form a part. Compression molding is efficient for creating solid and intricate components.
- Rotational Molds: Ideal for making large, hollow parts, rotational molding involves heating a mold while it rotates on multiple axes. This technique is popular for components like large storage tanks.
The Manufacturing Process of Automotive Molds
The process of creating automotive molds itself is a complex engineering discipline that includes several stages:
1. Design and Prototyping
The journey begins with the design phase, where engineers utilize computer-aided design (CAD) software to create detailed 3D models of the mold. Prototyping allows for validation of the design before full-scale production.
2. Material Selection
Choosing the right materials for mold construction is critical. Typically, manufacturers use high-quality steel or aluminum for their durability and resistance to wear and tear.
3. Mold Fabrication
Using advanced machining techniques, including CNC milling and electrical discharge machining (EDM), manufacturers shape the mold components accurately according to the specifications outlined in the design phase.
4. Assembly and Testing
Once fabricated, the mold parts are assembled. The assembled mold undergoes rigorous testing to ensure it meets all dimensional and functional requirements before being put into production.
Benefits of Utilizing Automotive Molds
The importance of automotive molds cannot be overstated, as they provide numerous advantages, including:
- Cost Efficiency: By enabling mass production, automotive molds significantly reduce manufacturing costs over time.
- Improved Quality: Molds ensure consistent product quality, as each piece produced adheres to precise specifications.
- Design Flexibility: Modern mold technology allows for complex designs and rapid iterations, accommodating innovative automotive designs.
- Reduced Waste: The efficient use of materials in molding processes minimizes waste, supporting environmental sustainability efforts.
Innovations in Automotive Molds
The landscape of automotive manufacturing is continually driven by innovation. Recent advancements in automotive molds include:
1. Smart Molding Technologies
The advent of smart molding technologies allows for real-time monitoring and data collection during the molding process. These technologies ensure optimal performance and facilitate predictive maintenance, enhancing productivity.
2. 3D Printing for Mold Production
3D printing has revolutionized the creation of molds. Rapid prototyping and the ability to produce custom molds on demand allow for faster development cycles and more tailored solutions for automotive manufacturers.
3. Advanced Materials
New composite materials are being developed that improve the strength-to-weight ratio of molds, offering enhancements to both mold performance and the quality of the final products.
The Role of Deepmould.net in Automotive Molds
As a leading provider of automotive molds, Deepmould.net combines years of expertise with cutting-edge technology to deliver high-quality, precision molds tailored to the automotive sector. Their commitment to excellence is demonstrated through:
- Customized Solutions: Deepmould.net offers personalized molding solutions that meet the unique needs of their clients, ensuring the highest level of satisfaction.
- Skilled Workforce: With a team of experienced engineers and mold makers, Deepmould.net excels in delivering superior quality molds efficiently and effectively.
- Continuous Innovation: The company works diligently to incorporate the latest advancements in molding technology, keeping their clients competitive in the fast-paced automotive market.
Challenges in Automotive Mold Manufacturing
Despite the advantages, automotive mold manufacturing also faces challenges:
1. High Initial Costs
Investment in advanced mold technology can be substantial. Although it pays off in the long run through efficiency and cost savings, the initial setup is often a barrier for smaller manufacturers.
2. Design Alterations
Changes in vehicle designs can necessitate frequent updates to molds, which can be time-consuming and expensive.
3. Quality Control
Ensuring consistent quality across large production runs is a challenge that requires rigorous quality control measures and advanced technologies.
The Future of Automotive Molds
The future of automotive molds looks promising, driven by ongoing trends in automation, sustainability, and technology integration. Key trends that are shaping the future include:
1. Automation and Robotics
As factories increasingly adopt automation, robotics will play a significant role in the mold manufacturing process, enhancing precision and reducing human error.
2. Sustainable Practices
With growing concerns about the environment, manufacturers are exploring sustainable materials and practices in mold production, aiming to reduce carbon footprints.
3. Advanced Simulation Techniques
Utilizing advanced simulation software allows manufacturers to predict and optimize the performance of molds before actual production, saving time and resources.
Conclusion
To summarize, automotive molds are a cornerstone of modern vehicle manufacturing. Their ability to enhance efficiency, improve quality, and adapt to innovative designs makes them invaluable in the automotive industry. Companies like Deepmould.net are at the forefront of this technology, continually pushing the boundaries of what is possible in mold manufacturing. As the automotive industry evolves, embracing new technologies and sustainable practices will be key to maintaining competitive advantages and fulfilling the automotive demands of the future.